Happy Grasshoppian Holidays 2021!
Don’t let the sunny sky deceive you. Although we can enjoy some comfortable temperatures here in Seville even in December, it is also Christmas season for us. The Grasshopper team wishes you happy holidays and an easier year 2022. Our work hasn’t finished yet so we will be back in January with recharged Hydrogen tanks. 🙂
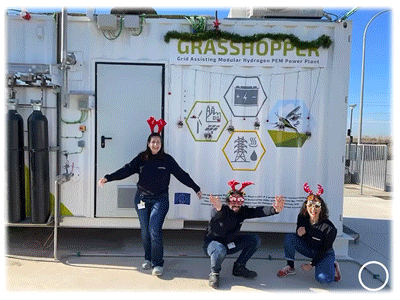
Grasshopper becomes famous!!!
Hydrogen is a trending topic; we all already know. In the Hydrogen rush, Grasshopper is not being left and is becoming famous!!!
As you know, the pilot plant is currently in Abengoa’s testing facilities, located in Free Zone of Seville (Spain), and once passed the start-up phase, the plant will be transferred to its destination in the Dutch city of Delfzijl.
Before the transfer is made, and motivated by the good results from the test (be patient, this will update in another post ), Grasshopper has triggered an institutional event. Both the mayor of Seville, Juan Espadas and the delegate of the Free Zone, Alfredo Sánchez Monteseirín, visited the plant last Wednesday. Naturally, they didn’t want to miss the opportunity to see first-hand the first of a new generation power plants. Power plants based on fuel cells can operate dynamically with rapid response, which allows them to contribute to developing a circular economy and zero-emission society providing grid stabilization services.
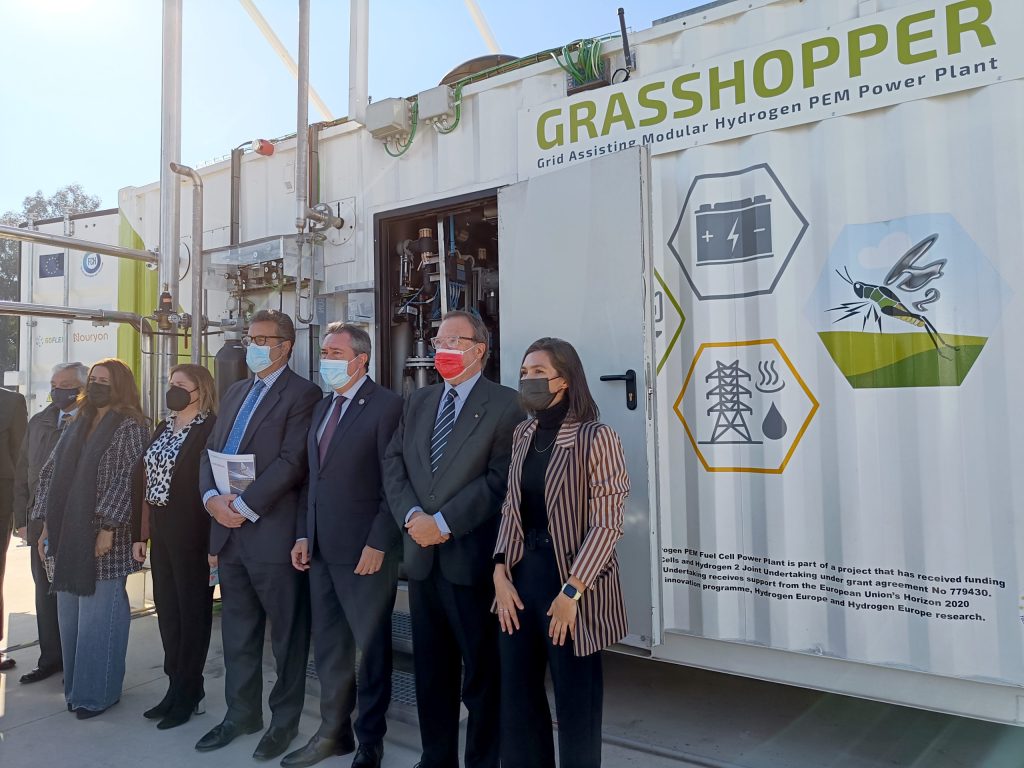
Grasshopper team made a quick presentation to understand the aim of the project. After that, a guided tour of the facilities by the Grasshopper technical team. The typical good weather from Seville, even in December, even improved the experience.
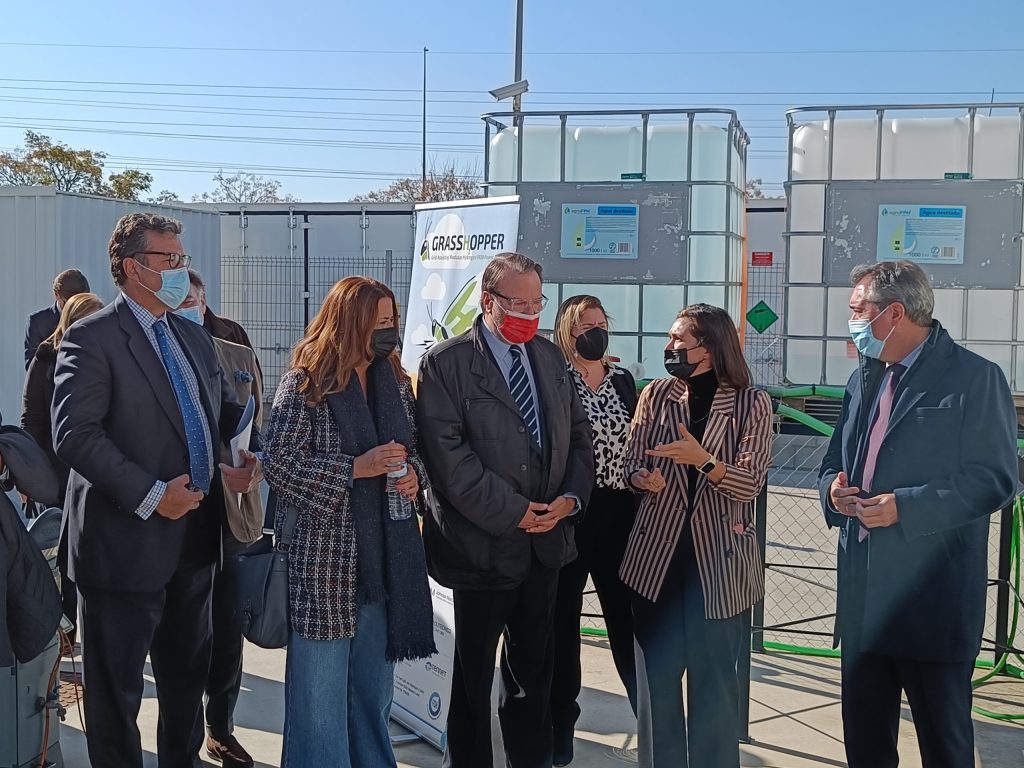
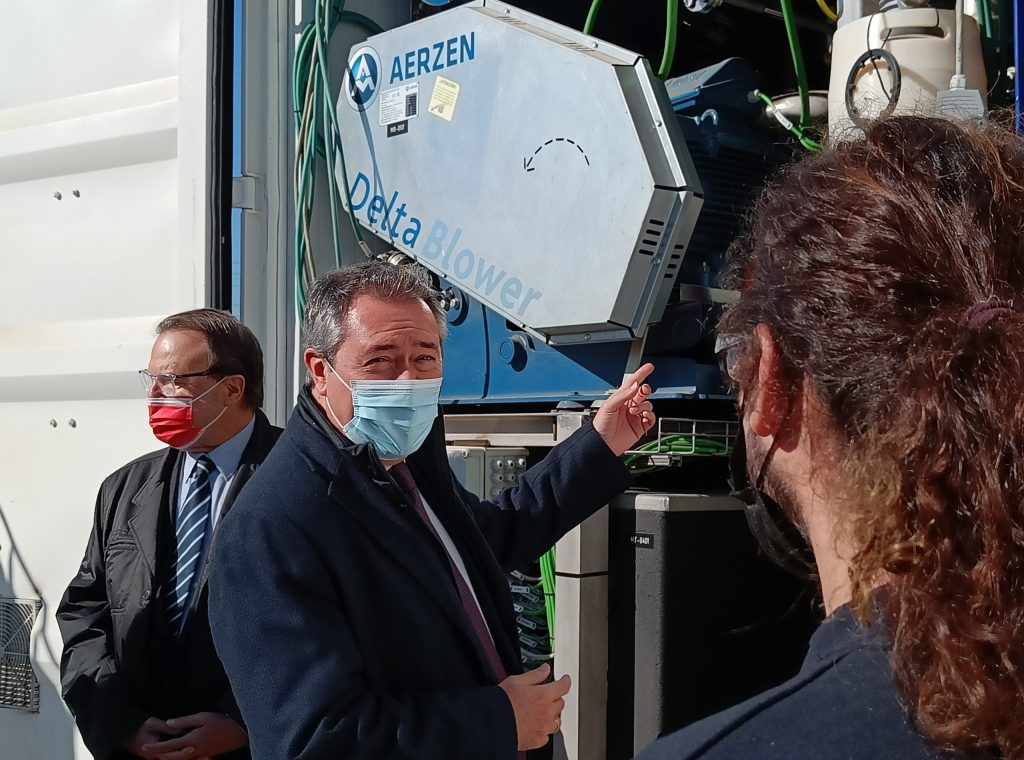
In the words of Juan Espadas:
“This is a powerful work of research and technological innovation that reveals the full extent of the talent that exists in the company Abengoa, which is a source of pride for Seville and Andalusia.”
Alfredo Sánchez Monteseirín emphasized that:
“In the coming years, we must accelerate the large-scale transformation of our energy system to achieve a 100% renewable, and therefore clean, design by 2050.
The press has been made of the event, and Grasshopper appears in many news! Here there are some links so that you can enjoy them:
Abengoa :: Press Room :: News :: News Archive :: 2021 :: December
But this is not the only appearance of the Grasshopper project in the media. Visit our press section for more mentions
We hope this is just the tip of the iceberg and Grasshopper continues to bring good news to the entire team!
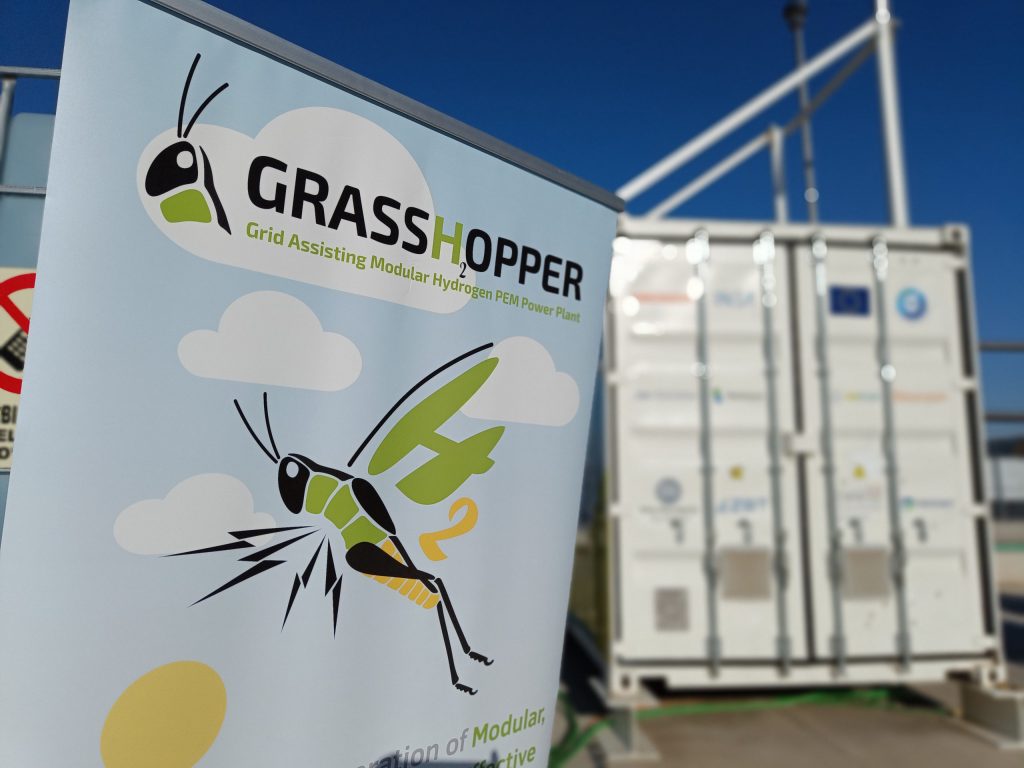
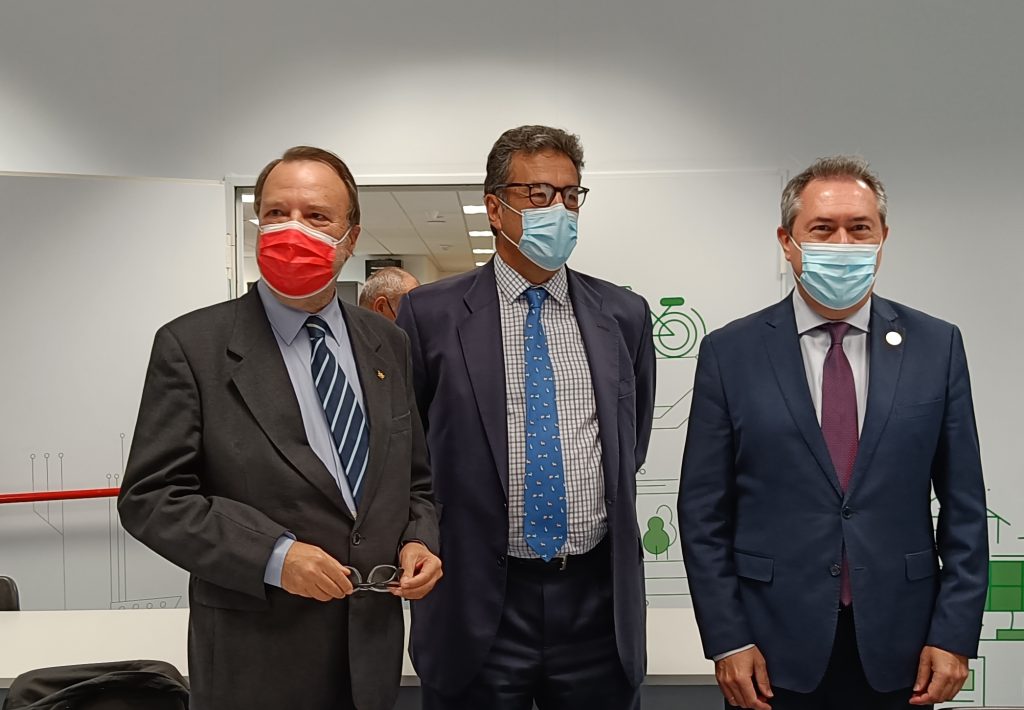
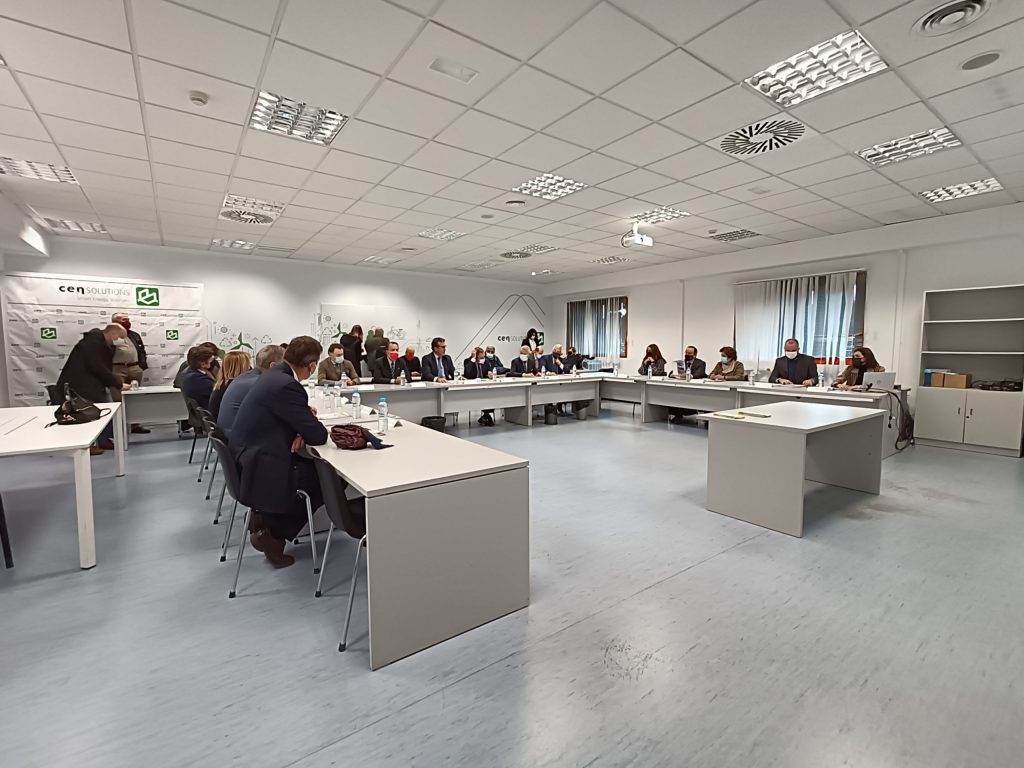
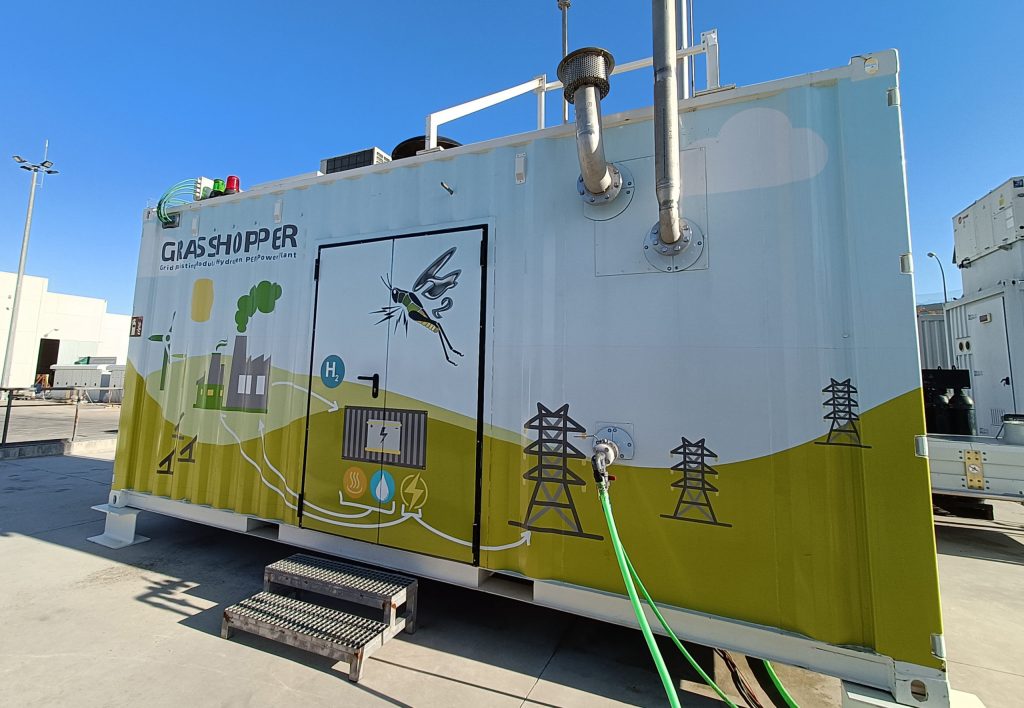
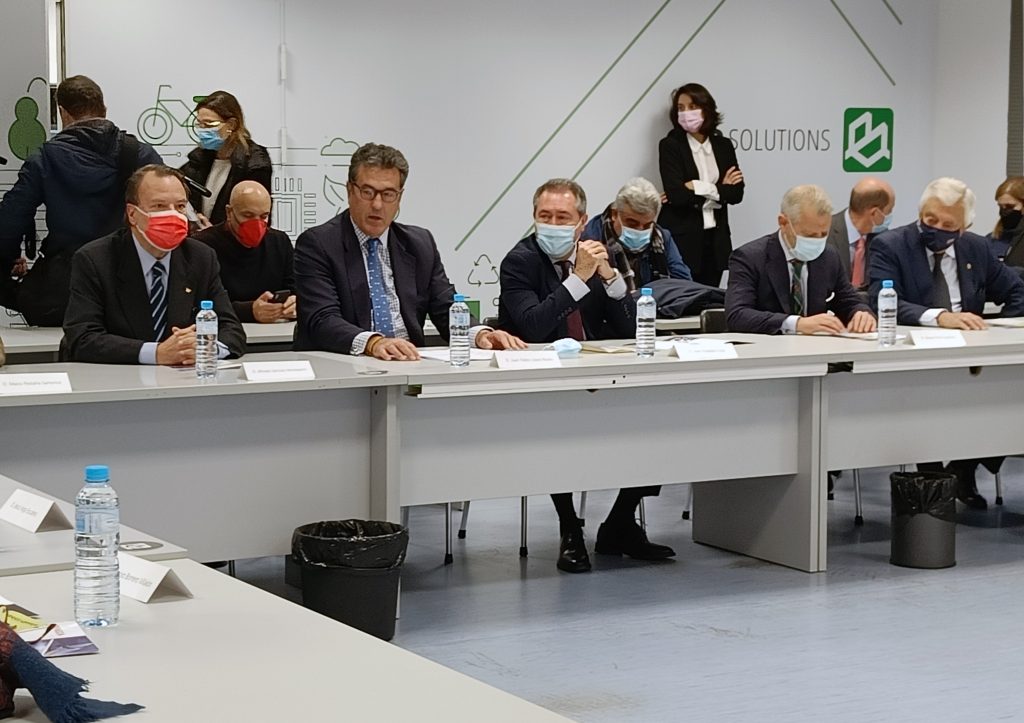
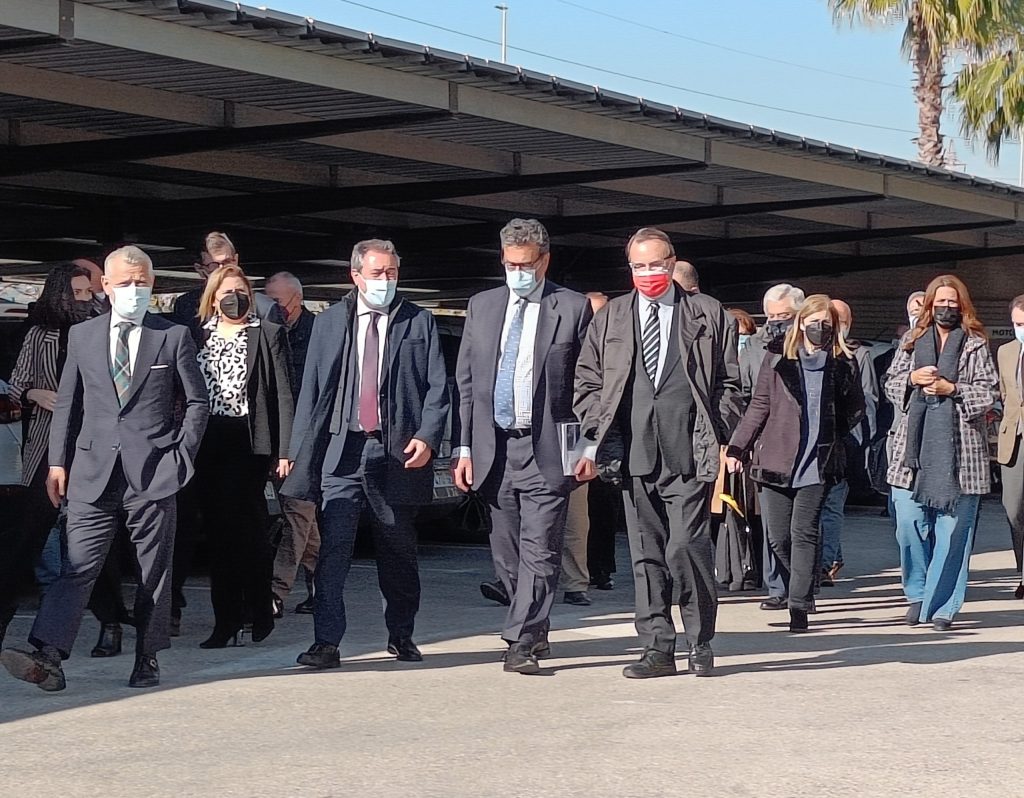
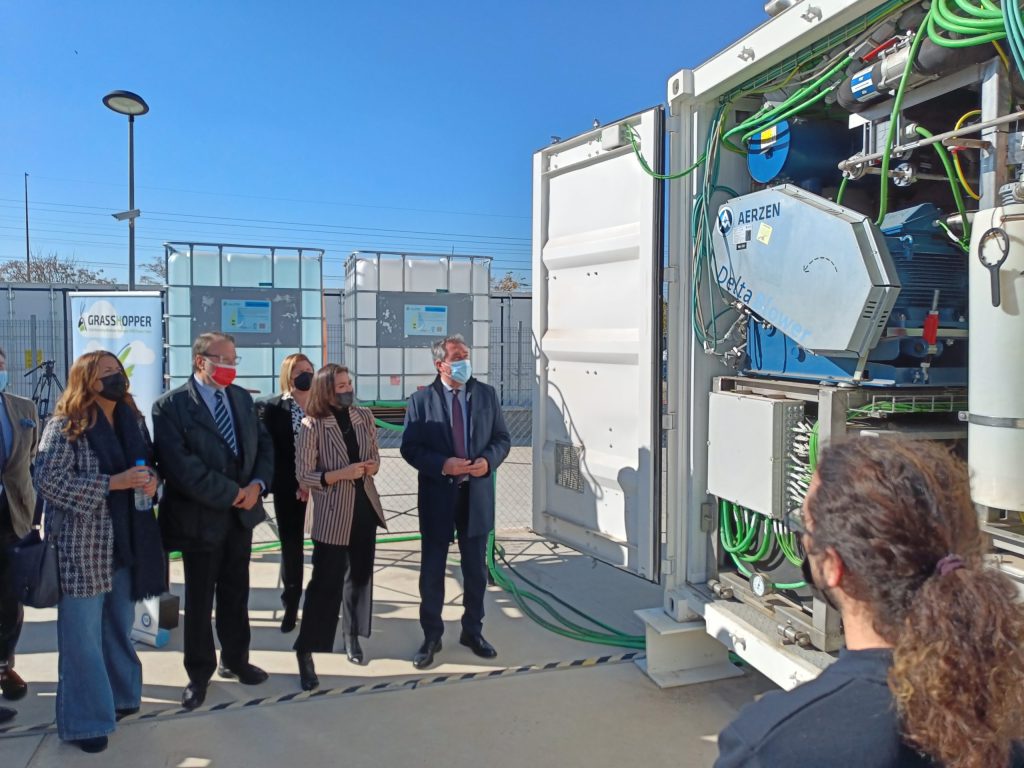
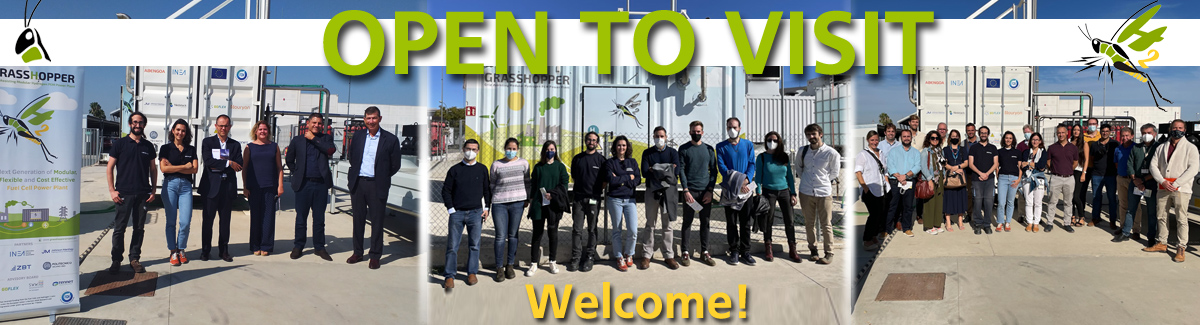
The pilot plant is OPEN to VISIT. Don’t miss out!
With most of the tests completed, there is lots to show and tell about the project. And the best to learn it all is to visit the pilot plant!
As the end of the project approaches, also does the transportation of the plant to its final site in Delfzijl, Netherlands. But before that, we want to make the most of the time while the plant remains in Abengoa’s testing facilities in Seville, Spain. So why not schedule a trip to enjoy the southern Mediterranean heat as winter approaches? Get in touch with us through the official mail info@grasshopperproject.eu or by our contact form here. If travelling is not possible for you at the moment, we invite you to participate in our webinar for virtual visit of the plant. We haven’t decided on a final date for it yet so make sure to keep checking our web for updates.
Both companies and institutions have already enjoyed the visit to the pilot plant . Including DSOs, Oil&Gas, universities… any interested parties are more than welcomed. Want to take a look? See the pictures below!
Read More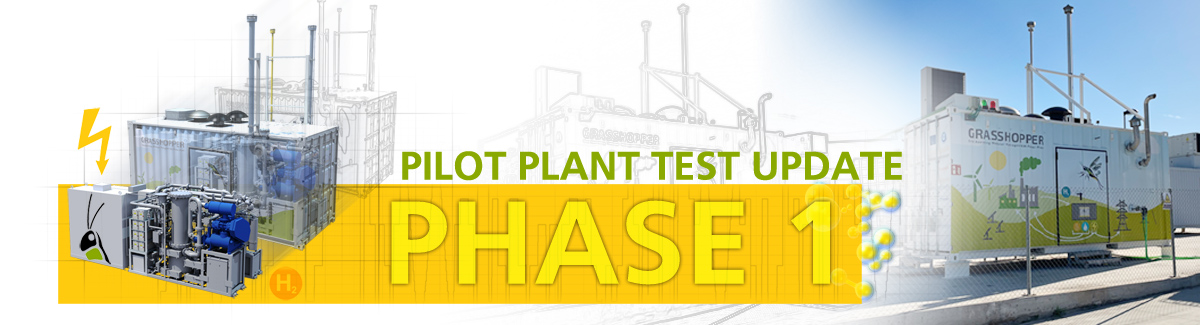
The Pilot Plant is Doing Great! – Testing Update
It has been a while since our last update. And not because the project has stopped, but quite the opposite! We have been experiencing quite busy months since the begging of the year. At this point, we have reached the final phase of testing in Abengoa’s facilities in Seville (Spain). And in a couple of months, and if Covid-19 allows it, the plant will be installed in the final site in Delfzijl (Holland), where it will remain operating for 5 years. So, lets go into details on what have been accomplished so far.
1st testing phase completed.
During the initial months of testing, we focused on the plant itself without having the fuel cell stacks installed. In this period no power was produced, allowing us to optimise control strategies and check for improvements without worrying about damaging the delicate stacks. Many different tests were carried out including the initial commissioning and functional tests of individual equipment. Most tests fall into the category of these three main types.
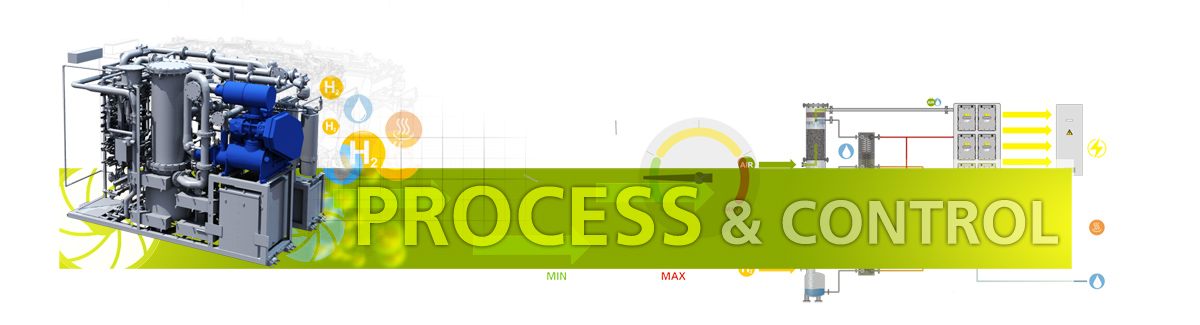
As with any other plant, commissioning comes first to ensure the correct functioning of all equipment and sensors. Several steps are performed :
- Verification of correct installation and electrical connection
- Scaling of communication signals and IO testing.
- Cleaning of circuits and equipment
- First “cold” start-up of individual components and actuators such as pumps compressors, valves…
- A preliminary control loop adjustments
Once all the components have been tested individually, it is time to start the subsystem functional tests. Apart from the development of new fuel cell stacks, the project aims to design an efficient plant that protects the stacks to expand their lifespan to the maximum. Including a dynamic, fast and pressurised operation. For that, a precise control is required. Testing each subsystem before the stacks are installed is therefore critical. It allows to test without worrying about damaging the stacks.
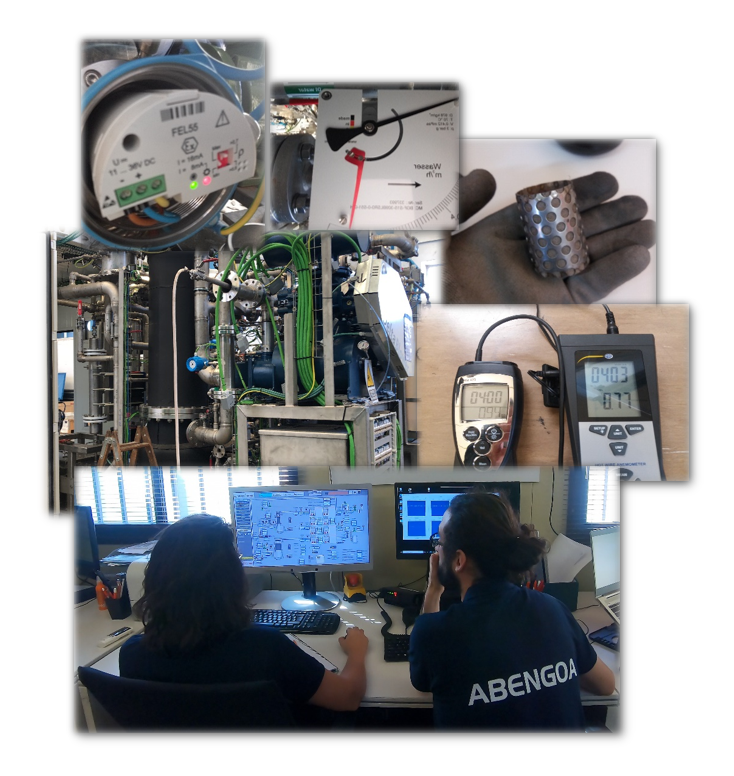
Air and Hydrogen subsystems.
Combines flow, pressure, temperature and humidity control to provide the best possible conditions of air and hydrogen to the stacks. More than 10 control loops and variables intertwine with each other. Advance control techniques such as smith predictors and multi-variable control were needed to accomplish all targets.
Cooling and utilities.
Since heat is provided by the stacks while generating power, thermal response of the plant was simulated to adjust the control. Moreover, other test were carried out as safety Nitrogen inertisation, auxiliaries consumption measurement, environmental control and anti-freezing features…
Control architecture and HMI improvements
Starting from the programming already developed during construction, a lot of effort and time has been invested into validating and updating it. With special effort on the HMI (Human machine interface), a key part of a correct plant operation.

One of the main topics that come to mind talking about Hydrogen Power Plants is safety. Hydrogen has sometimes a bad reputation of being dangerous. But, like any other fuel like natural gas or diesel, by making the adequate engineering decisions and following the safety standards created by industry experts, safe operation is assured. This is nothing new, many conventional industries have been safely working with Hydrogen since long back. And their experiences, with further innovations, are applicable to Hydrogen Power plants. In Grasshopper, safety has always been a core engineering focus, and of course, during testing even more. The safety analysis is, as a consequence, a continuous process that starts at the engineering phase, follows the construction, and finalises “as-built”.
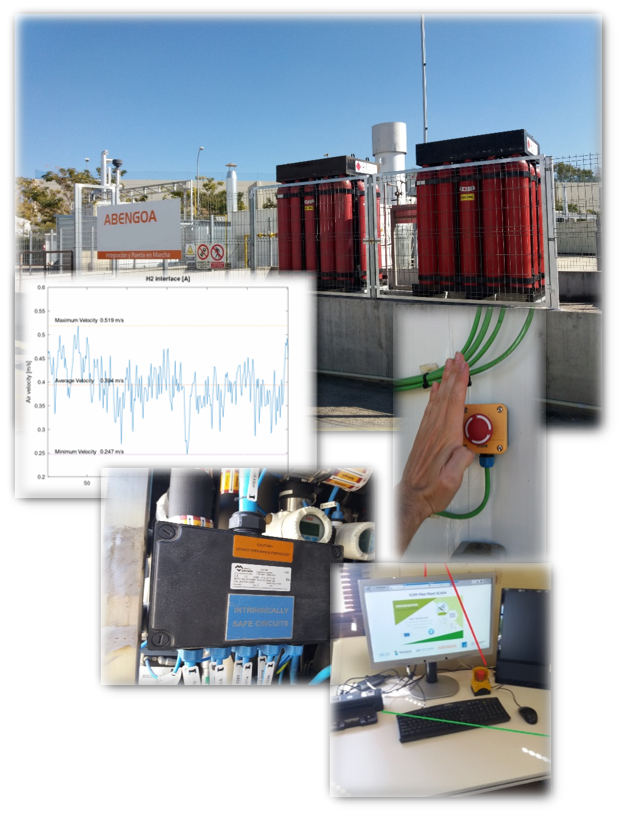
Verification of Intrinsically safe cabling and other ATEX certified equipment
Intrinsically safe instrumentation is just one of the type of ATEX certified protection available but most instrumentation and sensors are designed as intrinsically safe equipment. Which doesn’t store enough electrical energy to be a possible ignition source
Leaks detection
PEM fuel cells are permeable equipment, this means that there is an unavoidable leakage of Hydrogen around the stacks. This is usually called the stack’s “breathing”. Because of this, is very important to minimise and characterise the leakage rate of the system while the stacks aren’t installed. In any case, if anything happens that creates a hazardous atmosphere, fixed Hydrogen detectors are always monitoring the container. Additionally, hydrogen detection tape is installed around possible leak points for maintenance revisions.
Testing of emergency stops and safety subsystems
Several layers of control ensure a safe operation. Not only for personnel protection but also to minimise damage to the equipment in a “loss of control” event. If Hydrogen is detected inside the container, an emergency shutdown is performed. This eliminates any possible ignition sources maintaining ventilation. More over, the hydrogen subsystem is immediately inertised with Nitrogen.
Characterization of air renovation flow inside the container.
An interesting aspect of the safety analysis done for the Grasshopper is the study of air flow inside the container. From the beginning , the plant was designed to promote a preferential flow of fresh air that would carry any possible leaks away from potential ignition sources, quickly out of the container. During the testing phase, these initial engineering decisions were validated with a real flow analysis of the air inside the container. With over 30 points of measurement, we could characterise the air flow speed, direction and variability with ambient conditions. Creating a clear image on how the renovations of air displace and mix within the container, and where pockets of Hydrogen could potentially create when a leak occurs. It is basically like performing a “real CFD” with the plant itself.
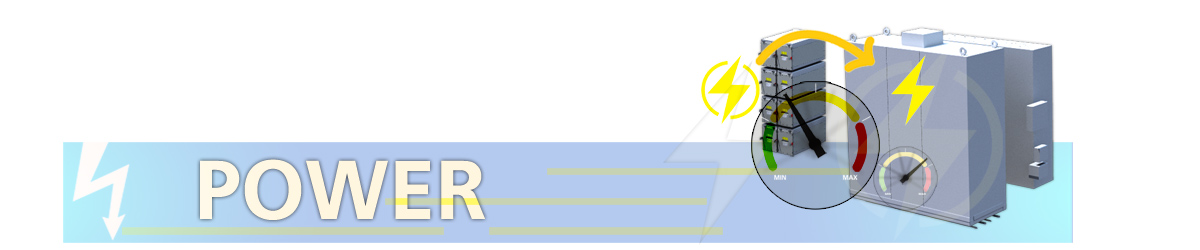
One of the main objectives of the project is participating in the reserve electric markets. To do so, a flexible and quick response of the plant is essential. As mentioned before in the process section of this article, it is important to do so without damaging the stacks. In this initial phase, we tested the PCS (Power Conditioning System), along with all the control strategies around it. Even though the plant was not generating power from Hydrogen at this moment, the rest of the system was operating as it would with the stacks. With the help of a DC source the real response of the fuel cells was also simulated.
Initial results show great response both in time and accuracy, complying with the energy request with just an error of 0.25%. The control system evaluates the energy request and translates it into a power setpoint that the plant will follow. Several variables accumulate and evaluate the produced energy along time. Allowing the plant to compensate for any mismatch. In the image below a typical response of the plant can be observed. From warm stand-by, the plant immediately responds to the energy demand. The control ensures that the total amount of energy exported matches the requested.
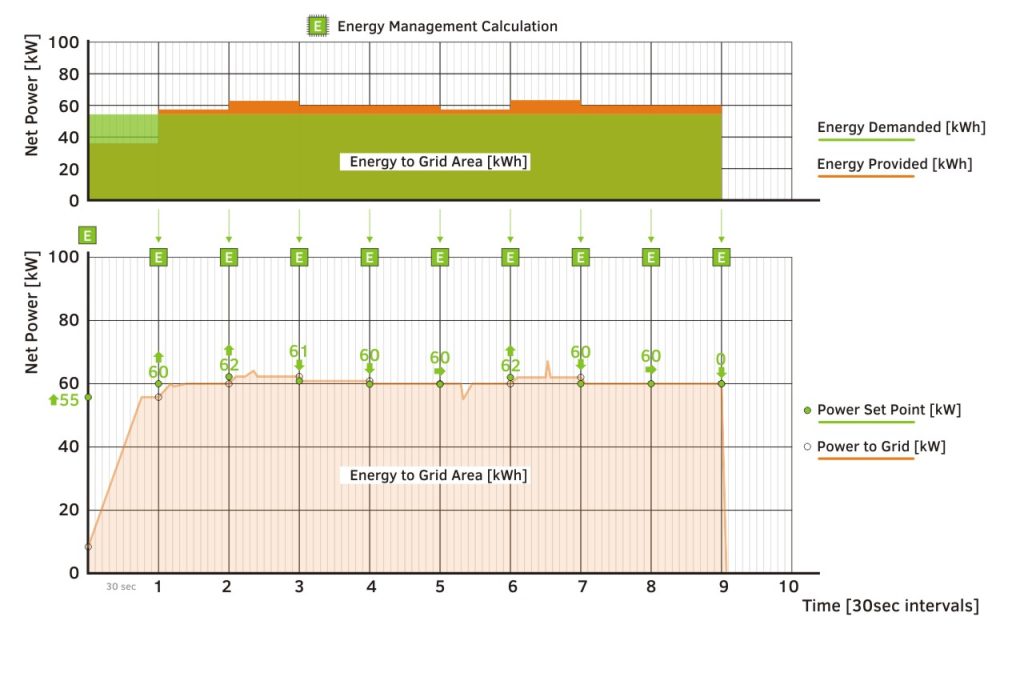
But all of this is only but a fraction of the tests carried out in this first phase. In the following weeks we will install the fuel cell stacks in the plant and power production will begin. Starting the second phase of FAT.
Read MoreFor a new year of prosperity and full of Hydrogen
From the Grasshopper Project we hope for a successful year 2021. There is no need to enumerate the hardships our society had to suffer during this 2020. And of course research and development was also affected by it. The ever-changing world is even more hectic these days, and can be easy to forget the always present need for green energy and a more sustainable future. But we are on it. For that reason, we would like to celebrate the new year with hope and optimism. Despite the Covid-19, all our members have been working hard to achieve our goals and I am sure many research projects feel the same way we do. Lets keep working hard to make this little marble in the universe that we live in a place to be proud of.
The Grasshopper team wishes you a year full of Hydrogen!
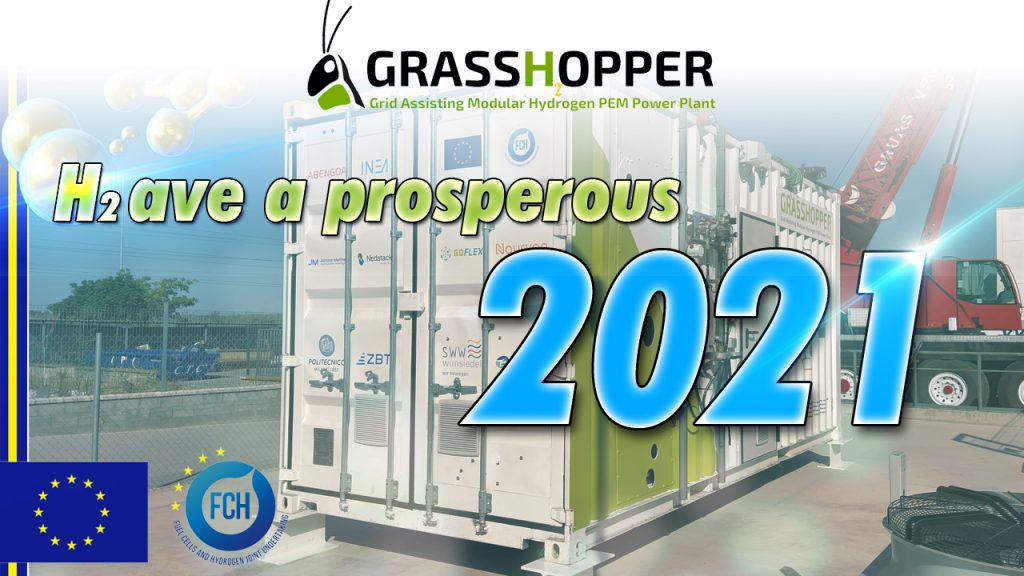
Flow Field simulations for a long lasting Stack
Fuel Cells are, in a nutshell, a REDOX reactor where a chemical reaction takes place. Therefore the correct distribution of reactants through the fuel cell is critical for a smooth operation. As a partner of the Grasshopper project, ZBT has focused a lot of effort on the design of optimal flow distribution. Including practical tests in their facilities in Duisburg, and very intensive 3D CFD flow field simulations.
This time, we want to share some of the results achieved on this topic. Specifically regarding the evolution of the flow in the channels when a blockage occurs. PEM fuel cells work at a reduced temperature, usually, around 70ºC degrees. This means that the produced water may condensate inside the channels of the stack, blocking the flow of Hyrodgen or Air in it. This could lead to fuel starvation, damaging the membrane where the reaction takes place. Therefore reducing the efficiency and life expectancy of the stacks.
A correct design of the channels and the GDL (Gas diffusion layer) are critical to mitigate this problem, and simulations are a great tool to reduce iterations and tests which are usually more expensive. In partnership with AVL, ZBT has carried out detailed 3D simulations of individual cells. Providing important information for the whole stack and the design of the flow field.
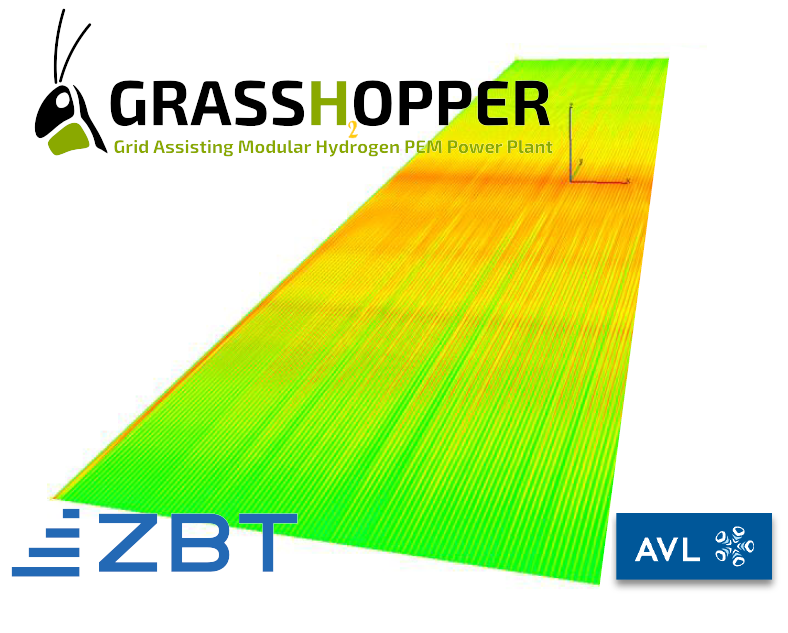
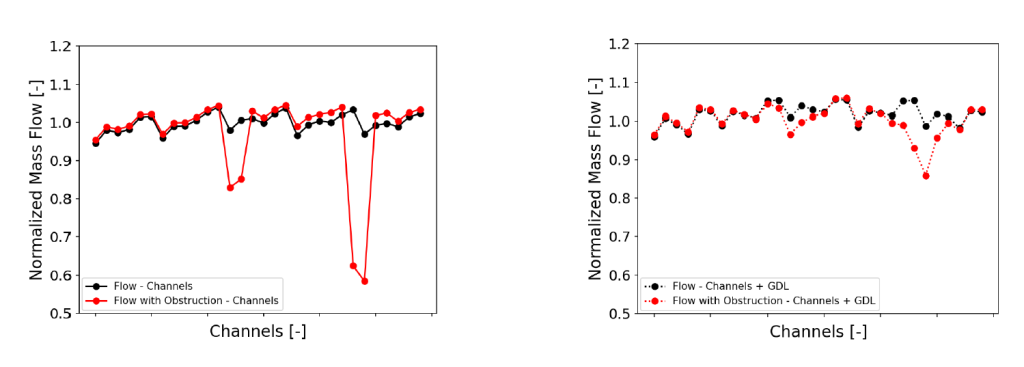
The results of the simulation show good promise towards developing a stack for maximized life expectancy. With a considerably reduced blockage impact of the condensate water in the channel flow. With this, Grasshopper is a step closer to reduce the Levelized costs of electricity produced on Hydrogen Fuel Cells in stationary applications.
Don’t forget to check more about this in the ZBT and AVL website.
Read More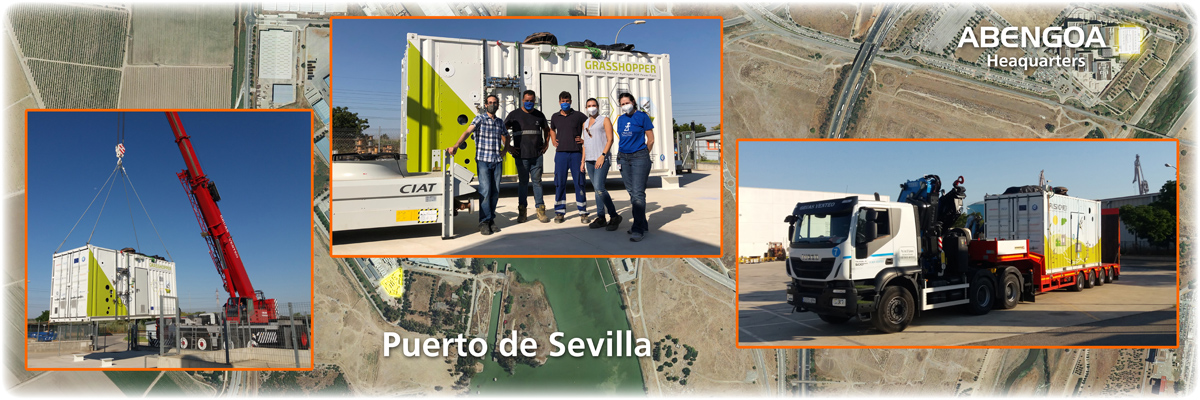
The Grasshopper pilot plant is ready for testing!
Last month, the construction of the Pilot Plant was completed! And at last, We moved it to Abengoa’s testing facilities in the port of Seville for the next phase. This is a major milestone towards the project’s success, and we are very eager to share it.
As we have mentioned before, check this post about containerized solutions, the plant can be easily transported and deployed at any location. The workshop where the plant was built was also located in Seville, so this transport only lasted about 30 mins through the outskirts of the city. But the process is identical if transported for very long distances.
Next month, Factory Acceptance Tests, or FAT for short, will begin in Abengoa’s testing facilities. Where many other technical innovation projects have also seen the light. Starting with IO Testing, following with circuit tests, or control loops adjustment among others, the pilot plant will be ready to receive the Fuel Cell stacks later this year. We will be sharing more about the FAT and how the tests are progressing along the road. For now, We hope you enjoy this video about the Grasshopper Pilot Plant transport!
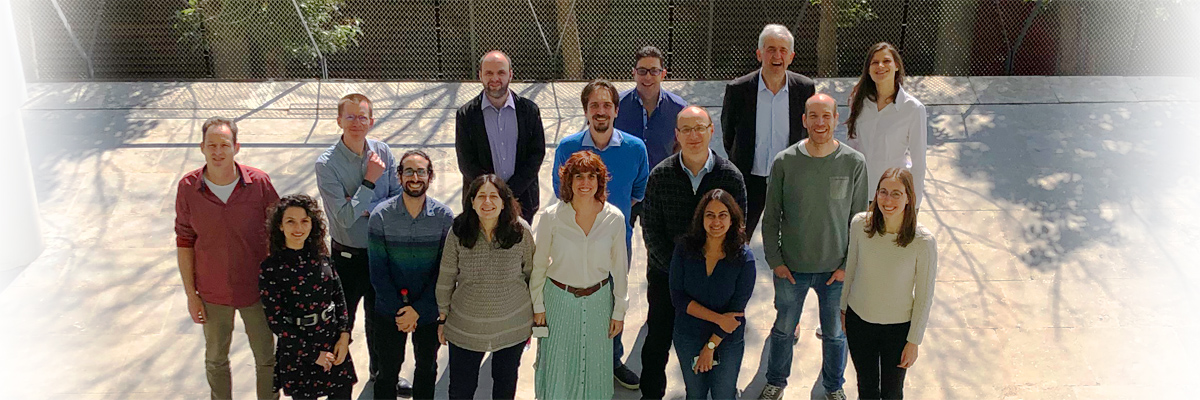
Periodic Consortium Meeting, Seville 2020
Like every 6 months, and as the construction of the pilot plant continues, the periodic consortium meeting took place. This time in Abengoa’s HQ in Seville in February 2020 from the 25th to the 27th. After reviewing the status of the project, the meeting was especially packed with lots of technical details and 1-on-1 discussions between the partners. Since the testing phase approaches, there were many details to go through together. And there is no better opportunity than a presential meeting. Some of the key aspects were the Grasshopper stacks development and the pilot plant construction. We also continued exploring the market applications for the resulting product. A process that started back at our consortium meeting in Duisburg last year.
This time the chosen location was Seville, Abengoa’s Headquarters, where the construction of the pilot plant was taking place. Not only to enjoy the much warmer winter weather of southern Spain but also to give the whole consortium an in-detail visit of the plant. We spent a good couple of hours in the workshop, inspecting and sharing details about the pilot plant and previous experiences. The construction will finish in the upcoming months. And finally, the testing period will commence!
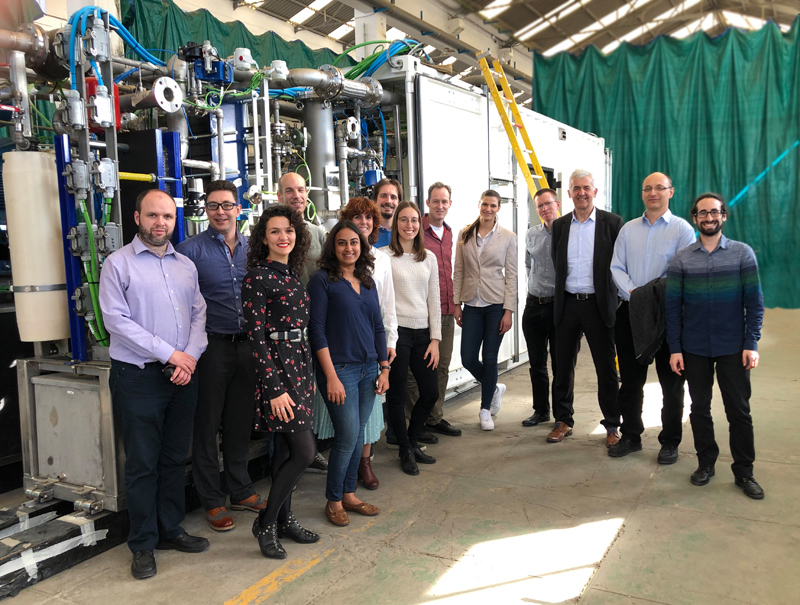
Read More
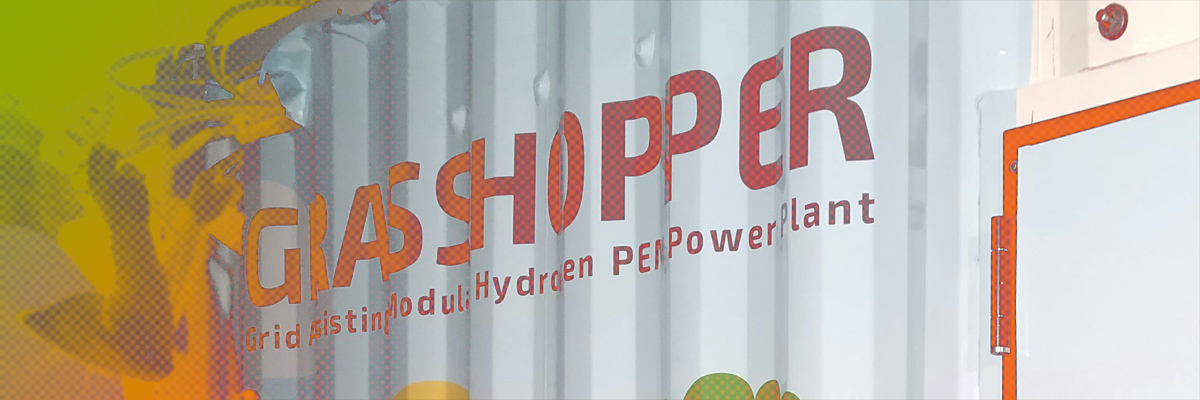
Because appearance matters, take a look at our exterior design
As we have discussed in a previous post, check it out here, there are many benefits of having our power plant inside a container. But one reason that was not talked much about, is that it can be easily disguised or beautifully displayed in public. Because there are no emissions and it has a reduced footprint, placing the plant in urban areas is more than possible. and for that, the plant needs to look good!
Of course, we didn’t want to miss the opportunity to demonstrate this with the pilot plant. So we have installed a full-size vinyl that not only makes the plant look very aesthetically pleasing but also serves as publicity for Hydrogen and Green Energy sources. With a simple and cartoonish style, one can, in a glance, see the whole purpose of the project and the possible applications of the Hydrogen PEM power plants by looking at the container.
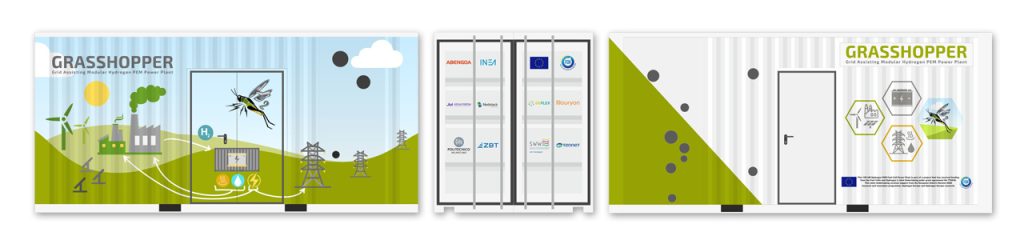
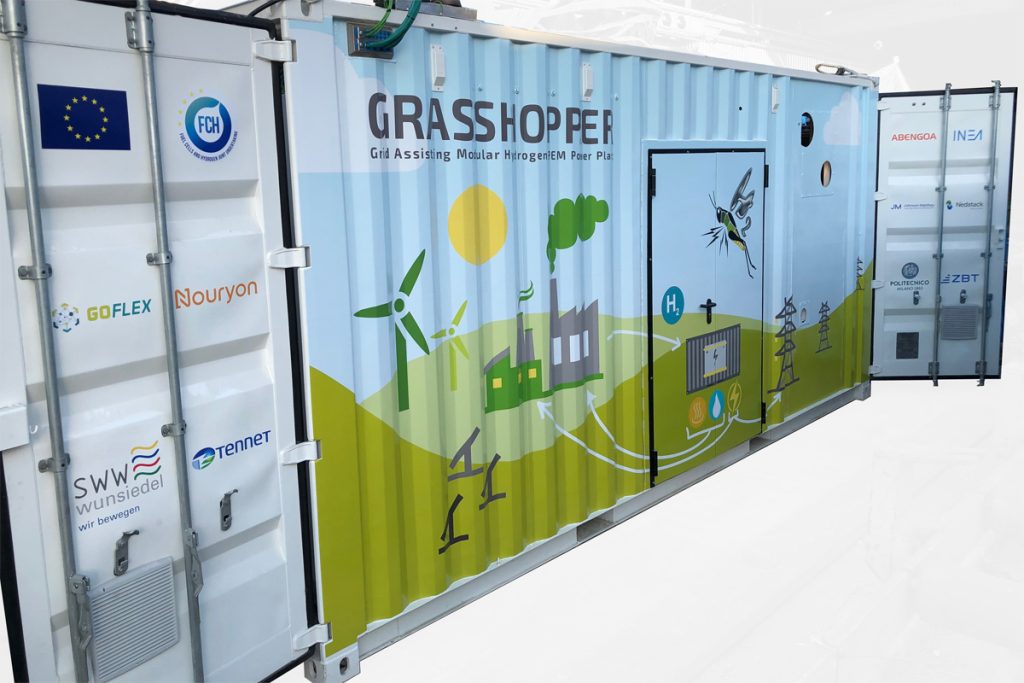
The previous images are the full design in the 3D model, first, and a real image of the container taken at the construction site prior to its completion, second. You can expect more of these pictures as the testing of the pilot plant begins in the following weeks!
Read More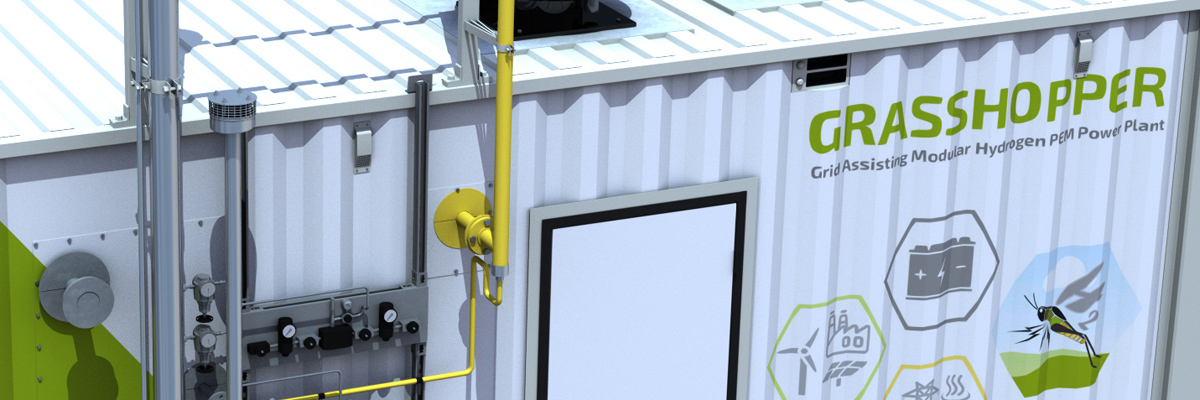
The 100kW Pilot Power Plant is under construction
As we approach the equator of the project, the construction of the 100kW pilot plant has begun. This is an important milestone for the project since many of the improvements designed on paper or laboratory scale will be tested and validated. But before we can do that, the pilot plant needs to be completed.
Like in the construction of any power plant, many different disciplines of engineering come together to create the final product. In our case, we have divided the construction into four main sections:
- Estructural: mostly regarding container refurbishment.
- Piping: equipment, instrumentation, etc.
- Electrical system: both the power conditioning system and auxiliaries.
- Control software development
With almost all engineering decisions made and 3D modeling ready, the construction can now begin. First, a standard shipping container will be modified to suit the project necessities. And once it is done, the installation of equipment and fabrication will continue until the plant is completed. Alongside the mechanical construction, the electrical system will also advance. All fitted into a 20 ft long container for rapid deployment and scalability. And lastly, the programming will put everything together, ready for a long period of testing.
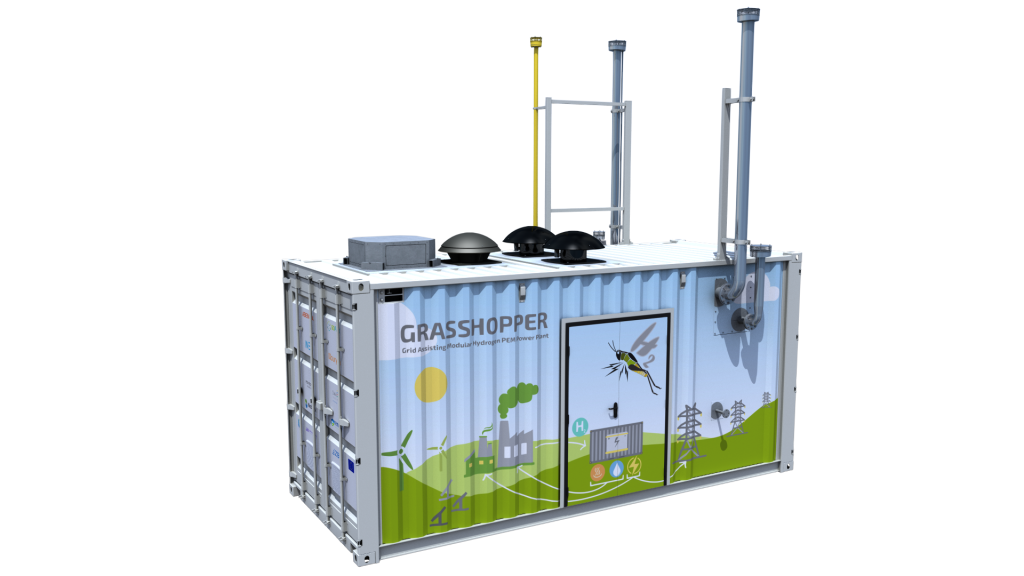
We are looking forward to receiving the first feedback directly from our workshop. Each step will surely reveal important improvements to take into account for the final MW design. We will keep you updated as things progress in our workshop with some interesting facts and news about the pilot plant construction.
Read More