Missed the webinar? Watch it online now
For those who missed the webinar that took place on 28th of March, there is no need to worry. The session was recorded and uploaded to Youtube. Or perhaps you want to revisit some interested data? Whichever your reason, you can re-watch the whole event right here. And don’t forget to contact us!
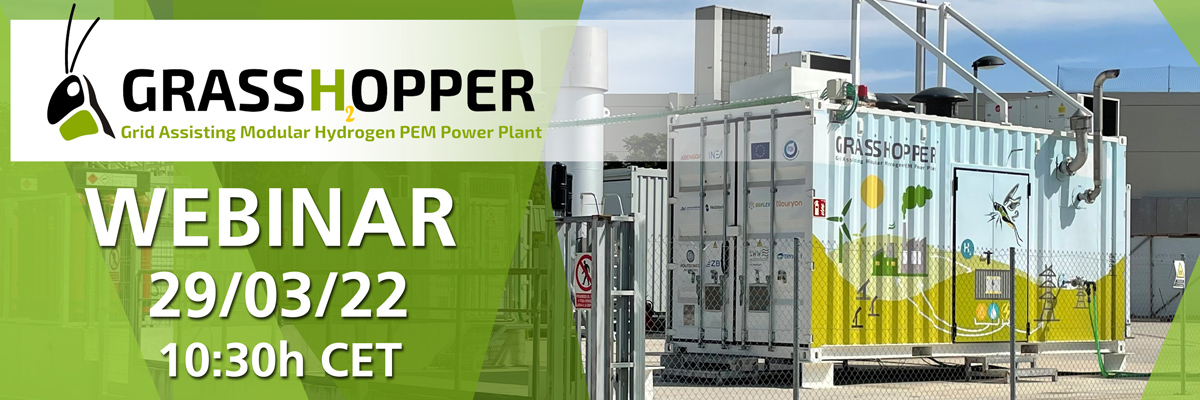
Project webinar – It is time to meet the team
After many months of hard work, setbacks and achievements, we are approaching the project end. During the last months, we have had the opportunity to present the project to some lucky groups that were able to travel to Seville and see the plant live. However, as it happened with any other aspect of our lives, covid prevents us from scheduling any live event. But there is always a bright sight! The grasshopper team has prepared a public webinar to share our learning and experience with the world. Here is a brief summary of the content you can expect in the webinar
- Overview of project goals and objectives
- Main results and achievement obtained so far
- Virtual tour to the 100 kW pilot plant
- Questions and interaction with the technical members of the project
There are limited spots, so be sure to register using the following link! Also, check out our new introductory video of the project, including a sneak peak to the pilot plant.
—> Register now here! <—-
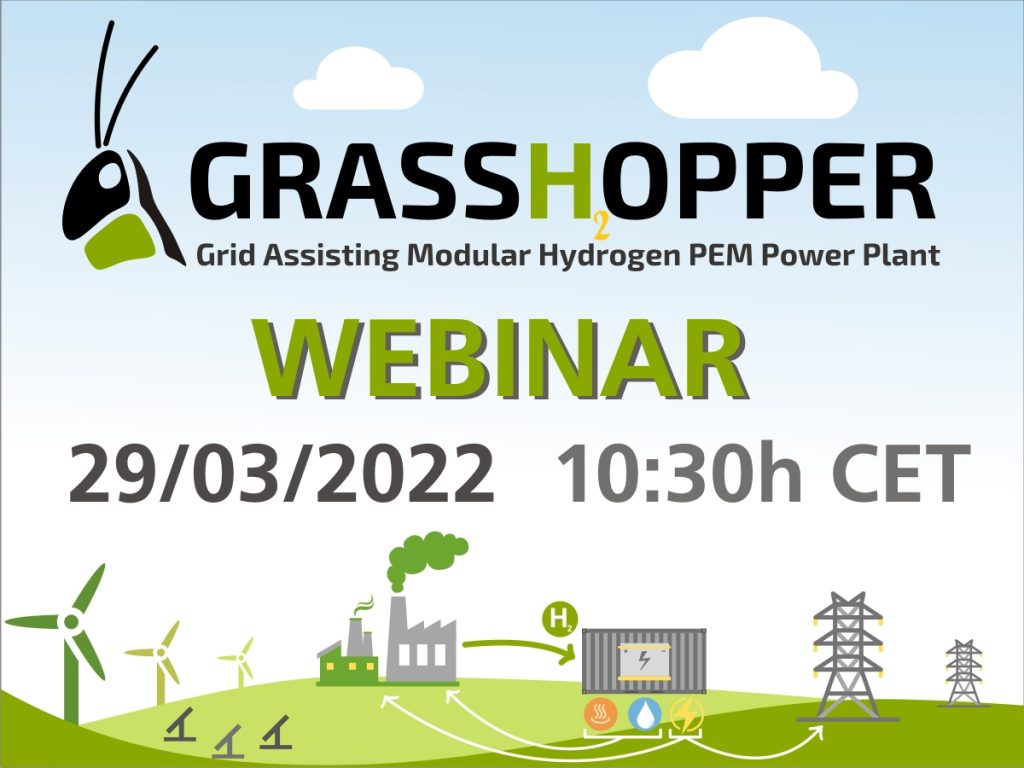
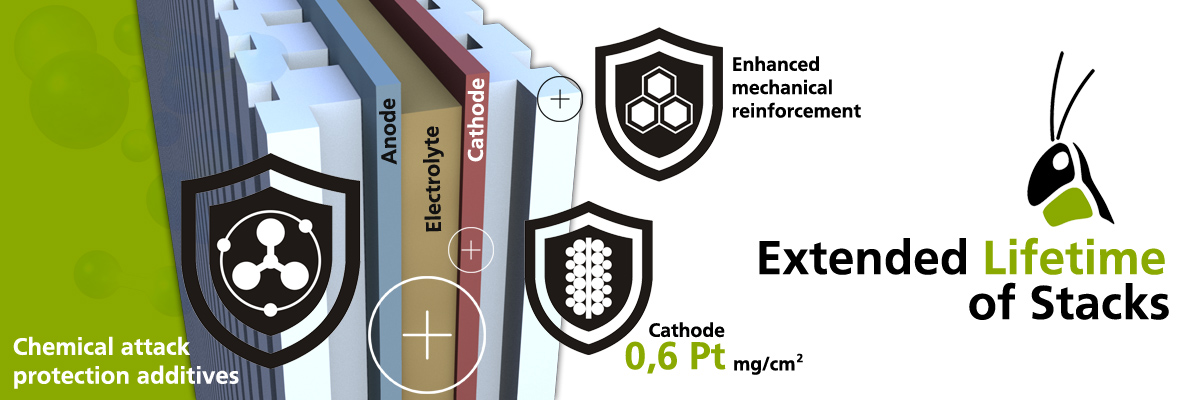
Initial performance results on new MEA – Built To Last
To achieve lower production costs and improve durability of Fuel Cell Power plants, it is essential to develop a new generation of MEAs (Membrane Electrode Assemblies). Johnson Matthey (JM) developed a new fuel cell membrane-electrode assembly (MEA) for a flexible, grid-supporting hydrogen power plant. To achieve the project objectives, JM’s MEA had to be durable, powerful, inexpensive and capable of flexible operation in response to changes in demand. Building on recent advances in automotive fuel cell technology and high volume manufacture at JM, it was possible to reach target manufactoring costs. Further enhancing the resulting MEA with measures to extend the lifetime.
The EU’s VOLUMETRIQ project (FCH-JU grant no. 671465) devised a drive cycle partly based on the New European Drive Cycle. A Drive Cycle is a series of data points of speed of a vehicle against time that is design to simulate the standard behaviour of vehicle. Applying it to fuel cells, the profile is transformed into current vs time. Its shape is shown below
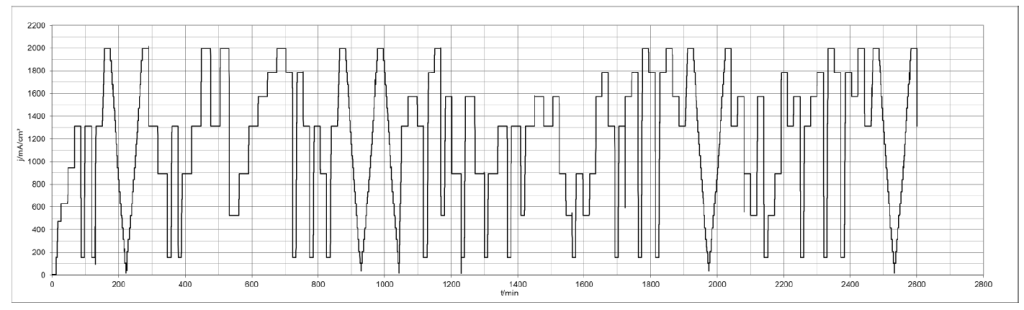
Due to its high varibility and changing load, is a great tool to evaluate performance and degradation of the membrane with load changes. The GRASSHOPPER MEA contained a 20 μm membrane electrolyte with a reinforcement, stabilised against chemical attack. As a result, the MEA showed a very high stability in drive cycle testing. The minimal loss of performance over the lifetime of the test, combined with a period of initial performance gain during CCM conditioning over time, led to near-zero measured degradation over 10 000 hrs.
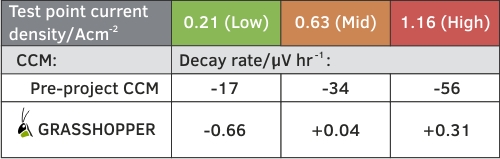
The developed MEAs are being built into stacks by GRASSHOPPER project partners Nedstack FCT, whose stacks power the 100 kW pilot-scale plant, assembled by Abengoa Innovacion. Operating the plant over its lifetime will allow us to gather real-world grid-assisting power data for this fuel cell technology.
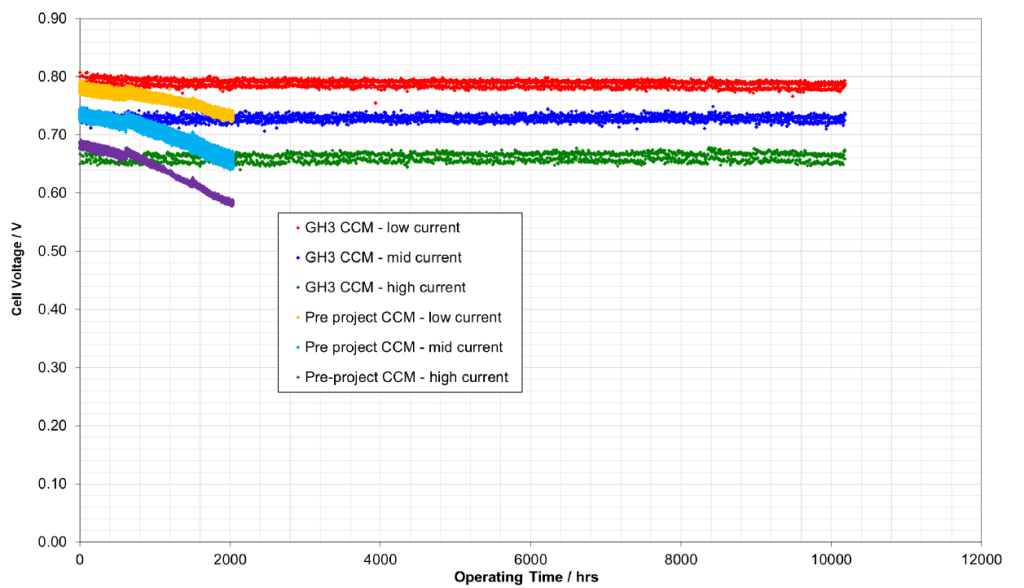
Results. A new section of our website
We have accumulated a good amount of results already. So its time to share them. As an European project, some of the data generated is labelled as “public”. Being our duty to make it accessible to the general population. For that purpose, we want to introduce you to the results section of the website. You can easily access it in the top menu and will allow you to download all the documents as we generate them. We distinguish between several types of document:
- Official European documentation.
- Scientific publications. Either in magazines, congress or similar
- Other interesting documents
During the last years, Politecnico di Milano, as a consortium partner, participated in the “Applied Energy Symposium: 100% Renewable” as well as other events. This particular event was a forum organised by the University of Pisa (Italy) to discuss and share the latest advancement towards a cleaner energy system. For said event, we published a paper titled: “Simulations of a flexible 100 kWel PEM Fuel Cell power plant for the provision of grid balancing services”. Where Polimi studies the potential capabilities of the pilot plant based on a computational model of the plant. This and other papers are already available in this section of the website, so keep checking it for updates!
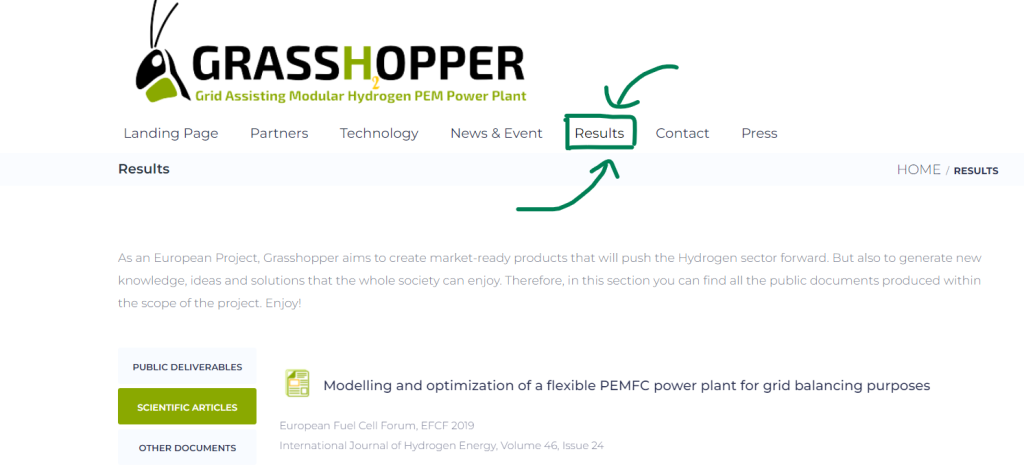
Flow Field simulations for a long lasting Stack
Fuel Cells are, in a nutshell, a REDOX reactor where a chemical reaction takes place. Therefore the correct distribution of reactants through the fuel cell is critical for a smooth operation. As a partner of the Grasshopper project, ZBT has focused a lot of effort on the design of optimal flow distribution. Including practical tests in their facilities in Duisburg, and very intensive 3D CFD flow field simulations.
This time, we want to share some of the results achieved on this topic. Specifically regarding the evolution of the flow in the channels when a blockage occurs. PEM fuel cells work at a reduced temperature, usually, around 70ºC degrees. This means that the produced water may condensate inside the channels of the stack, blocking the flow of Hyrodgen or Air in it. This could lead to fuel starvation, damaging the membrane where the reaction takes place. Therefore reducing the efficiency and life expectancy of the stacks.
A correct design of the channels and the GDL (Gas diffusion layer) are critical to mitigate this problem, and simulations are a great tool to reduce iterations and tests which are usually more expensive. In partnership with AVL, ZBT has carried out detailed 3D simulations of individual cells. Providing important information for the whole stack and the design of the flow field.
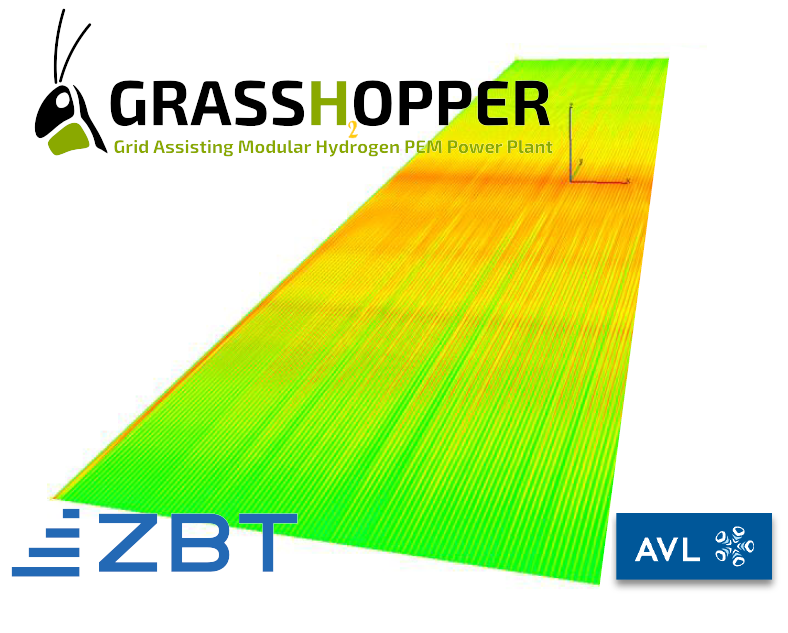
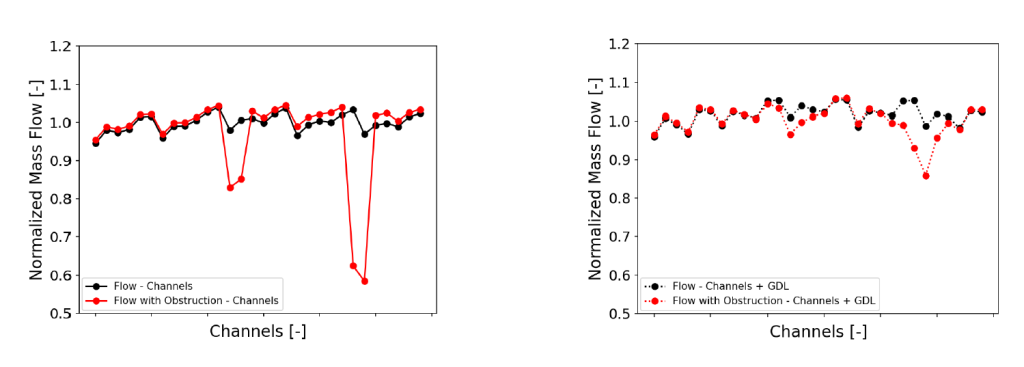
The results of the simulation show good promise towards developing a stack for maximized life expectancy. With a considerably reduced blockage impact of the condensate water in the channel flow. With this, Grasshopper is a step closer to reduce the Levelized costs of electricity produced on Hydrogen Fuel Cells in stationary applications.
Don’t forget to check more about this in the ZBT and AVL website.
Read More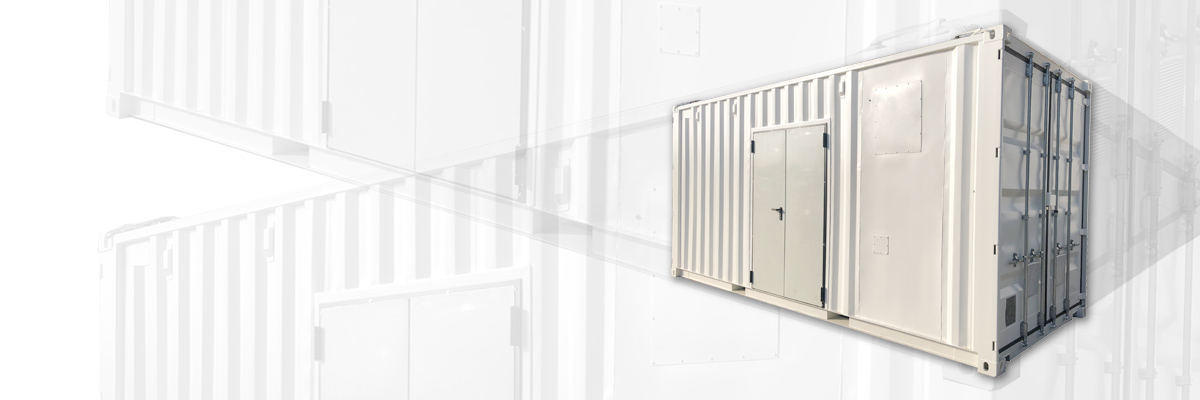
Why containerized Hydrogen Fuel Cell Power Plants make sense?
With the implementation of green energy alternatives and energy storage, there has been an increasing trend in using containerized solutions in those technologies that allow it. And not only Hydrogen PEM power plants, but many technologies have also joined this trend. One main reason for this is the great appeal of the “plug&play” philosophy, highly appreciated by the purchaser of the technology. But there is more than that for why a containerized Hydrogen Fuel Cell Power Plants make sense, and we would like to share it with you.
Scalability
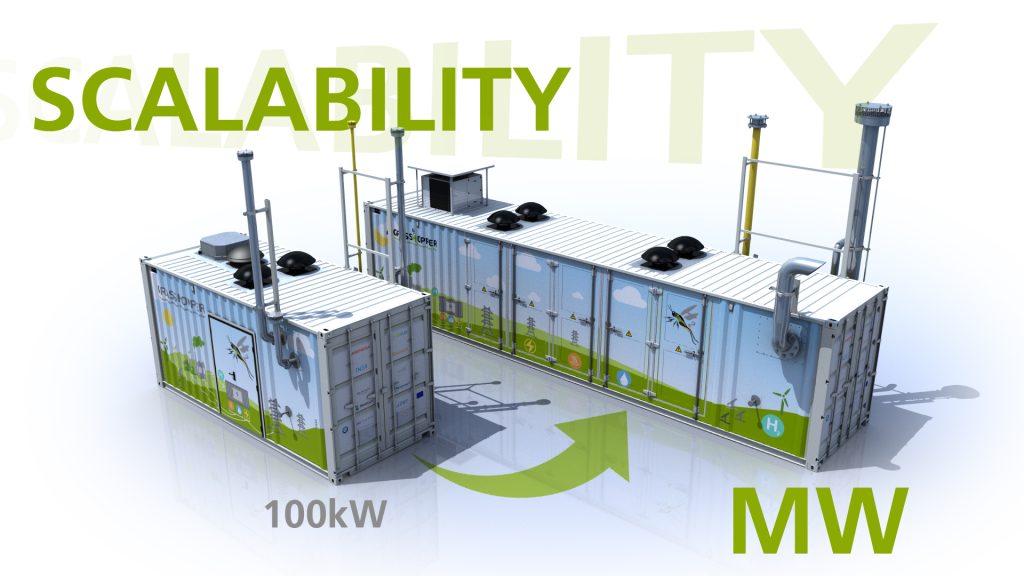
As the validation of the 100kW pilot plant finishes, We will carry out a MW scale design incorporating all the knowledge accumulated through testing. Even though the distribution of equipment inside may differ, the overall design doesn’t change much. In fact, the pilot plant has been designed for scalability. More power means increasing the number of stacks installed in the container. But since all stacks share the same design, it is a simple “copy-and-paste” process. Adding additional racks and gas distribution manifolds. Not all equipment scale at the same rate, therefore, space can be optimized with larger designs.
Modularity
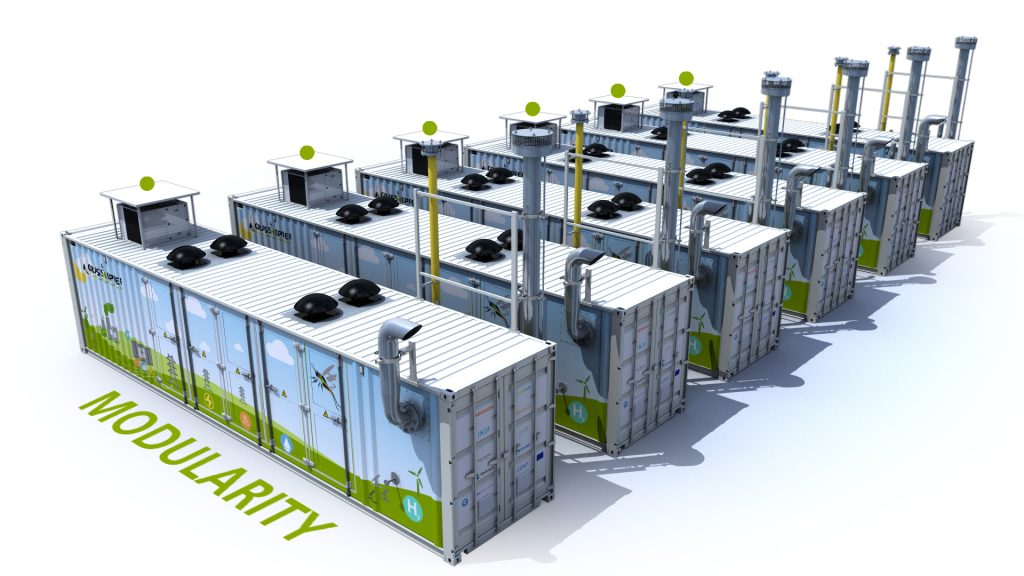
In a similar fashion, when the MW design is optimized and containerized, increasing the power of the plant is as easy as using multiple containers. Modular systems can be built, shipped, and installed quickly. This is ideal for the current increasing demand for Zero Emissions power systems. With an adequate sizing of the Hydrogen supply line and grid connection, multiplying the power is as easy as installing another container next to the previous ones. Adding a higher layer of control, adequate interaction between each unit can be achieved for maximum performance and efficiency, or maximize the lifetime of PEM stacks.
Easy transportation and Plug&Play
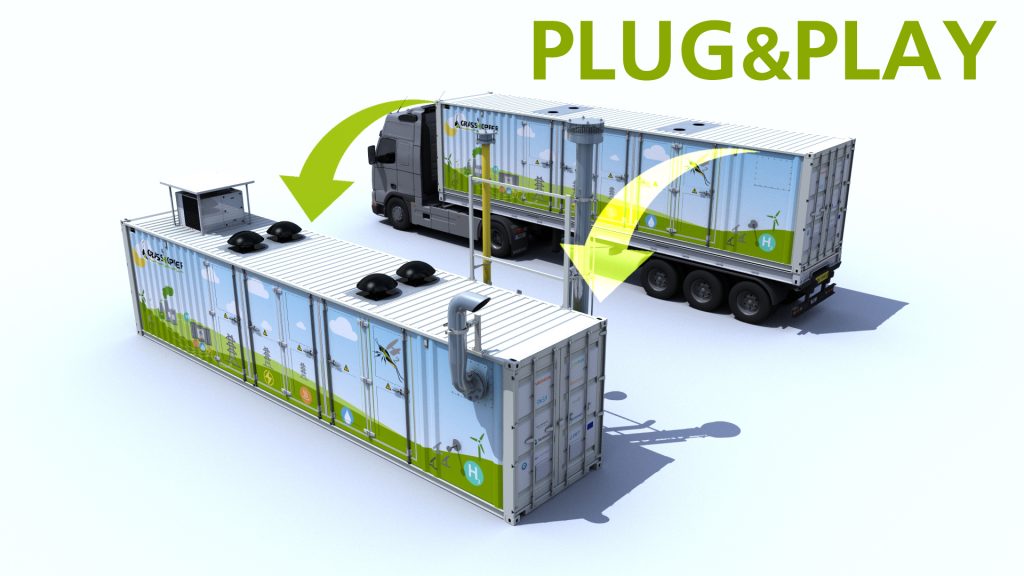
Probably the most noticeable benefit of having the plant inside a standard container is easy transportation and its quick installation. And this provides important flexibility. Containerized Hydrogen Fuel Cell Power Plants can be used in remote locations such as islands, mines, temporary buildings, encampments… Even as emergency generation units for many different applications such as data centers or hospitals. Providing a Zero emission alternative power source for such special needs. More and more of these plants are being installed in hard-to-reach places, or where the regular delivery of fuel has become prohibitive.
Not only that, but with a containerized solution, installation greatly simplifies. Forget about complex site preparations or connecting multiple units of different suppliers. Just drop the plant where you need it, connect the media and electrical interfaces and you are good to go. The electrical system, control architecture, and process, everything is packed inside. Since the container walls include these connections, no work, or minimal work, is needed inside the plant.
Transformation
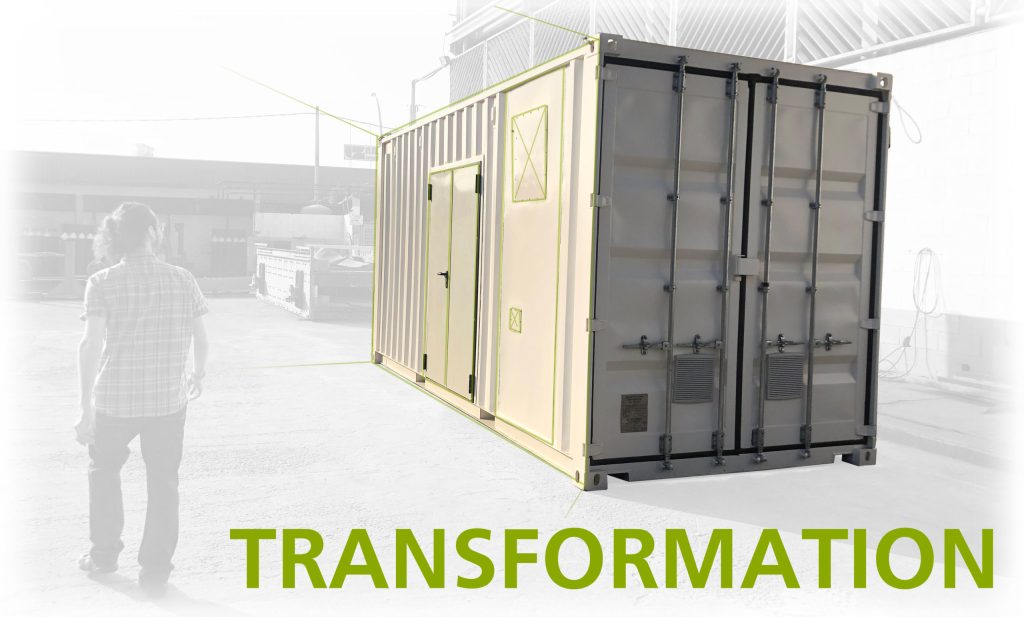
Last month, we finished the refurbishment of a standard shipping container to accommodate our needs. In the pilot plant, we have divided the container into two hermetically sealed sections. One for the electrical compartment and one for the process compartment. Media connections transverse the wall of the containers and junction boxes on the outside minimize the work inside.
The next question that arises with these units is regarding maintenance. Having all the equipment packed inside a container greatly reduces the footprint as we mentioned before, but it also reduces the available space for maintenance. This flaw can be overcome by designing an “extractable” unit. In case of a major maintenance operation, all equipment is pulled out of the container with a simple procedure. Then maintenance takes place outside.
Read More